High vacuum pumps: The heartbeat of advanced applications
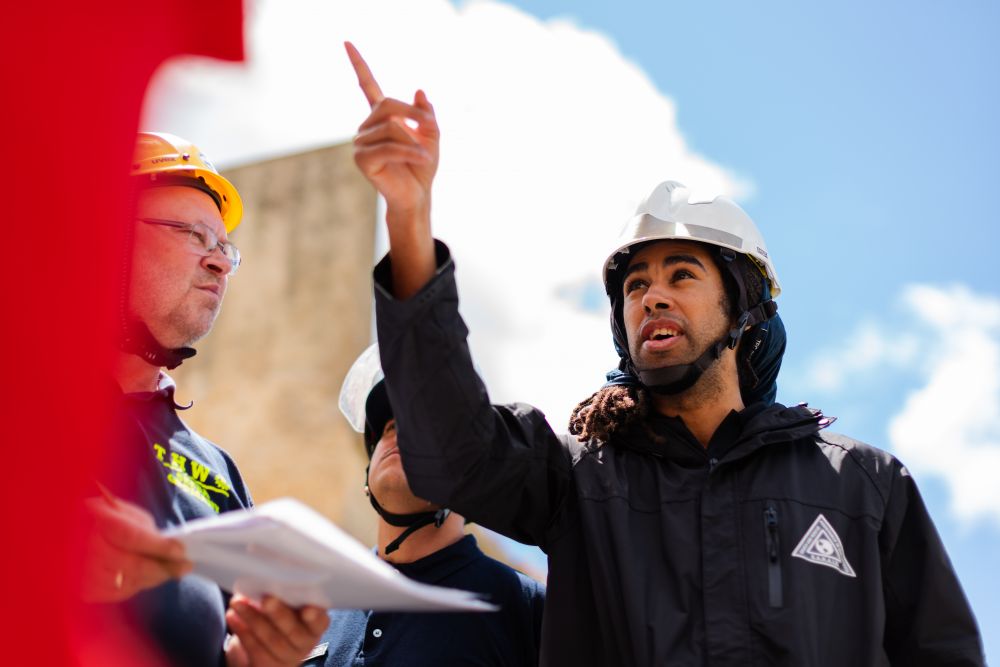
Industrial and scientific advancements have long been powered by the force of suction and pressure. At the core of these essential processes lies the high vacuum pump a key device responsible for creating vacuums greater than the typical range. These advanced systems are not just components; they are the very heartbeat of various sophisticated applications, where creating a near-perfect vacuum is imperative. This article delves deep into the world of high vacuum pumps, their operational principles, applications, and where to find expert solutions for all vacuum needs.
The basics of high vacuum pumps: Understanding the technology
A high vacuum pump is a device that removes gas molecules from a sealed volume, leaving behind a partial vacuum. This state is essential for many modern technologies and scientific practices. There are several types of high vacuum pumps, each differing in method and suitability for specific applications.
The two primary categories of high vacuum pumps are gas transfer pumps and entrapment pumps. Gas transfer pumps, such as rotary vane and turbo-molecular pumps, function by mechanically moving gas molecules out of the chamber. In contrast, entrapment pumps capture gas molecules on surfaces within the pump via processes such as cryogenic condensation or chemical reaction.
Differentiating between the types of high vacuum pumps is vital as it determines their suitability for various tasks. For instance, turbo-molecular pumps are excellent for applications that require a clean vacuum environment since they do not release any substances back into the vacuum chamber.
Applications of high vacuum pumps: From laboratories to industry
The use of high vacuum pumps spans across a myriad of fields. In the realm of scientific research, they are indispensable in physics experiments where particle-free environments are required, such as in the operation of electron microscopes and particle accelerators.
In the industrial sector, high vacuum pumps are critical for processes like vacuum coating, where a thin film of material is deposited onto a substrate. This method is used for reflective coatings on glass, creating barrier layers for food packaging, and producing solar panels. Semiconductor manufacturing also relies extensively on high vacuum pumps to create the cleansed atmospheres necessary for the production of microelectronic components.
Additionally, these pumps are pivotal in the field of aerospace engineering, where they play a role in space simulation chambers, testing components in conditions mirroring the vacuum of space. Such diverse applications underscore the versatility and essential nature of high vacuum pumps in modern technology and development.